Untitled (Autoprojettazione, 1123 xE/1123 xR), 2004
courtesy kurimanzutto
As I’ve said before, the first Enzo Mari autoprogettazione furniture I ever saw was by Rirkrit Tiravanija. He had tables and chairs fabricated from polished stainless steel, which his gallery from Mexico City, kurimanzutto, showed at Basel and a couple of other fairs a few years ago.
They weighed a ton and cost a fortune–as furniture, anyway; as sculpture, they seemed like a bargain–but they looked spectacular.
Rirkrit hit a zone in his work then where he was re-creating various examples of modernistic furniture and architecture in mirrored stainless steel; there was a ping pong table; several corner assemblages using three Smithson-esque, non-site mirrors; and an entire chrome pavilion in Bilbao. The effect was to simultaneously aestheticize the original and dematerialize the substantial object on display, turn them into non-objects. Which is kind of ironic, since they’re among the most atypically beautiful works the supposedly non-object-oriented [heh] artist has made.
See another picture at kurimanzutto, slide 4 [kurimanzutto.com, image above, too]
Tag: autoprogettazione
Enzo Mari x Ikea Mashup, Ch. 4: Finish Fetish
For the 2002 reissue of his 1974 catalogue, PROPOSTA PER UN’AUTOPROGETTAZIONE , Enzo Mari added “a few technical hints.” I love them, especially the quotation marks, even as I prepare to ignore them a little and end up with something less “belle” than it could be:
…Then, from a purely formal (symbolic) and “instructive” point of view, table tops are “attractive” [“belle”] if they are made by putting several small planks together. From a strictly utilitarian point of view you can use plywood or chipboard.
For the same reasons the constructions are “attractive” if they are left rough, with the saw marks, neither planed nor varnished.
I found this slightly obsessive discussion of finishing solid pine furniture to be quite helpful, if a little daunting. But already, it saved me from myself and helped me lift my wood finishing sights beyond the lying corporate shelves of Ace Hardware:
First, however, a warning is needed: there is zero ‘truth in advertising’ in the finish industry. Absolutely anything can contain absolutely anything, no matter what the label says. There are products out there labelled tung oil that don’t have any tung oil whatsoever in them. Many ‘tung oil’ products depend mostly on phenolic resins. You have to buy from a source that is expert enough to know precisely what is in their products and trustworthy enough to tell you. In Canada, that’s Lee Valley, in the USA, Sutherland Welles.
Sounds good to me.
Sure enough, the extremely helpful folks at Sutherland and Welles guided me toward the right product for the project, a table with a top that will see regular use. I expect I’ll have enough polymerized tung oil varnish and sealer to give the table a good five coats, if not the 10-12 that Sankey prefers.
Meanwhile, I mapped out each piece to be cut onto the Ivar shelf components with blue tape. I plan to cut everything to length, finish the parts while I can reach all the corners, and then assemble the table. And then give it a last coat or two for good measure.
The wood cost $120, the tung oil, $82.
Enzo Mari x Ikea Mashup, Ch. 3: Decisions, Decisions
So I’m finally going to make my Enzo Mari autoprogettazione table from Ikea components. A publicist from Ford had offered a Flex station wagon for a road trip, and last weekend, I took them up on it. Which meant I could bring back the 89-in pieces of wood I’d scoped out. So I did. Next I will cut and finish the pieces. Then I will assemble the table.
Continue reading “Enzo Mari x Ikea Mashup, Ch. 3: Decisions, Decisions”
Enzo Mari x Ikea Mashup, Ch. 2: Parts
In the early 1970’s, Enzo Mari suggested using 1-by pine lumber to make his autoprogettazione furniture because it was cheap, standardized, easy to cut, and universally available at the corner hardware store. Now, my local hardware is a Home Depot, and the boards they sell come from New Zealand. So in keeping with the spirit of Mari’s design, I’m going to use components from Ikea furniture kits instead.
The dining table I’m going to make is called either F or EFFE, depending on which plans you look at [Mari’s own autoprogettazione book uses the former; Peter Stamberg’s 1976 blueprint anthology, Instant Furniture, which reproduces four of Mari’s autoprogettazione designs, uses the latter.] It calls for wood in two sizes. The truss and leg structure is made of 1×2 in lengths ranging from 10 1/2″ to 51″. The top calls for four 79-inch 1×8 planks, which actually comes to about 30″ across. [After it’s dried and finished, 1×8 boards are usually 3/4″ x 7 1/2″. I had no idea.]
There turns out to be far fewer useful sources of lumber in Ikea than I originally thought. [The idea hit me when I passed giant warehouse shelves filled with rolled up pine bed slats.] But most of the pine pieces in Ikea furniture are only 1/2-inch thick, too thin to use for underpinning a table.
Though I stuck to pine on principle, there is some solid wood furniture, mostly birch, with some oak. But by far, most of the wood-looking furniture is made from veneered particleboard; who knows what’d happen if you cut it?
I don’t doubt you could make a quintessentially Ikea Mari table by using only these kinds of components; the sleek, plastic-over-sawdust goodness of Ikea’s signature Lack tables and shelves could make for a very conceptually tight mashup, but that’d be the second or third piece I’d make, not the first.
The other major constraint is the length of the boards for the top; only three products have decent width pine boards within range of 79 inches [which is 200cm, if you’re wondering why Mari picked that length]. The 5/8-in. thick sides of the tallest Trofast storage units [above] are either 11 3/4 in. or 17 in. deep, but only 69 in. tall. And some of them have regularly spaced grooves for sliding bins.
[Though it felt like cheating, I did check out readymade tabletops. The Vika Furuskog tabletop comes in pine, and is 78 3/4 in. long, but only 23 5/8 in. wide; too narrow to use, too wide to double up on.]
The new Mandal bed [king-size, $249] comes really close to being the perfect Mari table kit. It has a smoothly sealed headboard and footboard of solid pine, which, on the king size model, are each 78 in. long. The headboard is 23 1/2″ wide, and the footboard is 12″; placed top-to-top, they’d be 35 1/2″ wide, which isn’t too far off. As a bonus, they have both taper on the bottom edge, which would be nice on the underside of the tabletop. [There is a row of pre-drilled holes along the base of each piece, though, which kind of bugs.]
Mari’s table calls for more than 66 linear feet of 1×2 wood underneath. It’s close, but the Mandal’s inner support rails may provide enough wood without buying extra pieces. The siderails are smoothly finished, too, and each 78 in. piece is 3 in. wide on the outside face, tapering to 2 in. wide on the inside face. The unfinished pieces underneath the bed are either 7/8 x 1 3/4 in. [i.e., 1×2], or 1 3/4 square. Four 1 3/4 sq. pieces are 27 1/2 inches long, just 1/4-in. longer than the table leg specs. If more wood is needed, a $20, twin-sized Sultan Lade bed slat offers one of the best options for raw wood. The 15 slats are 2 3/4 x 3/4 x 38, with slightly beveled top corners.
The Mandal has the added benefit of being factory sealed with a smooth acrylic finish. If it’s important to stick close to Mari’s original idea of unfinished wood, the far-and-away winner is the Ivar storage system. Ivar’s component-based, which means the shelves, side units, and corner posts may be all you need to make a table.
One pine top shelf [$19] is 3/4 x 11 3/4 x 82 5/8 inches Cut off the embedded metal brackets from each end, and it’s right at 79 inches. There’s also a vertical piece to cut off [or to not attach in the first place; the shelf I saw didn’t have it at all.] If you use three shelves, the table will be 35 1/4 inches wide, which adds 5+ inches to the horizontal pieces underneath the table, too.
Corner posts are 1 3/4-in. square and filled with drilled holes [$8, $12]. The side units are their own standard dimension–1 3/4 x 1 1/4 inches–which could be pulled apart and used as lumber. But it’s also tempting to use the ladder-like pieces whole. Both parts come in 70 1/4″ and 89″ lengths [$12, $15].
Maybe you could cut down [sic] on the sawing required by just making the table to Ivar’s dimensions instead of Mari’s. Then instead of a lengthwise shelf, you could build a top from shorter 33 x 11 3/4-in. shelves [$6] set crosswise.
I sit here trying to juggle the variables to the best effect: faithfulness to Mari’s original design; faithfulness to his concept, which is not quite the same thing; the inherent “Ikea-ness” of the inputs; the quality and utility of the output; the amount of tweaking, finishing, and labor required. And I repeatedly find myself creating a conceptual justification for the path of least resistance. All conceptual stunts being equal, I’m drawn toward the one that involves the least labor and mess. Which turns out not to be the same as requiring the least time, cost, or effort, as the 8-month over-analysis of making a simple table attests.
Enzo Mari x Ikea Mashup, Ch. 1
I wrote a few months ago about making a dining room table following Italian designer and theorist Enzo Mari’s 1974 Proposta per un’autoprogettazione, roughly translated as “A Project for self-design.” Mari’s goal was to effect a critical examination of the objects around us and the system of design, manufacture, distribution, marketing, and commerce that brings them into being. He did this by developing blueprints for a houseful of furniture that could be made from standardized pine lumber, in a day or two. The designs require only the simplest saw cuts and a hammer. And if you get the lumberyard to cut the lengths for you, it just requires a hammer. As Mari explained in an interview:
these items are not intended as alternatives to industrial ones, their creation is intended as a sort of critical exercise on design, and this is the reason why this experiment was called home design, not home production. The user, in repeating the operation, which can never be a slavish repetition…the designs have no measurements and while you are making them you can make changes, variations…when making the object the user becomes aware of the structural reasoning behind the object itself, therefore, subsequently he improves his own ability to assess the objects on the market with a more critical eye.
The EFFE table I want to build requires two sizes of board: 1×2 inch pine for the structure, and 1×8 planks for the top. In 1983, Mari explained that, “As regards material, the easiest to acquire is undoubtedly still the wooden plank.” Undoubtedly. So I headed down to the nearest hardware store, where there were several hundred varieties of curtain rod finials, but no lumber. I was told I could order pine boards of these dimensions, and they’d come in about a week. Couldn’t my contractor get wood for me? So I went to Home Depot, which had pine boards in several grades and dimensions. They were all from New Zealand.
First off, it wasn’t that nice-looking, but buying processed wood from the other side of the world in a 100,000-sf store seemed to contradict the spirit of the autoproggetazione project. Under those circumstances, Jeff Bezos’ critical response to the furniture design industry made more sense. [When he started Amazon, he made the desks out of hollow-core doors and sawhorses, a scrappy tradition the company continued.] But I didn’t want the aggressively cheap improvisation of a Bezos Table in my house.
The place where I saw the biggest piles of untreated pine lumber was, ironically, Ikea. The warehouse section near the store’s exit has palletsful of bookcases, chairs and beds, all flatpacked and ready for assembly [home production?] What would happen if you treat Ikea as your corner hardware store, and use their flatpack-optimized, mass-produced furniture components as the raw materials in an entirely different design?
Looking through the Ikea hacking communities, it seems no one had tried to make an Enzo Mari table from Ikea parts before. While Ikea publishes detailed dimensions for their assembled products, there’s no information on part specs. Over the course of several trips to Ikeas outside New York and Washington, DC, I identified every Ikea product that looked like a promising source of pine parts, and I measured each piece of wood.
Though there are many pine products at Ikea, there are just eight products or series whose parts come close to standard 1-by lumber dimensions. I’ll put them in the next post. Then I’ll calculate the various combinations to figure out things like the optimum use of material, the least amount of cutting, the cheapest/most expensive, the closest to Mari’s design, and the most successful table. We’ll see how it goes.
related: the 2002 reprint of Autoprogettazione from Corraini is much harder to find than it should be [abebooks]
previously: Autoprogettazione: The Making Of An Enzo Mari Dining Room Table
Autoprogettazione: The Making Of An Enzo Mari Dining Room Table
The economic and ecological and aesthetic far-sightedness of Enzo Mari’s 1974 Autoprogettazione still blows my mind. Translated variously as “self-projects,” and “self-design, self-made,” Mari’s collection of designs for furniture you could build yourself with just a hammer using cheap, off-the-shelf lumber anticipated several key design principles that resonate right now: DIY; sustainability; small-scale, local production and consumption; simplicity; handmade; hacking commercial products; and the open-source/creative commons movements [the furniture could be built by anyone except a factory or a dealer.]
Mari intended his Autoprogettazione to be made of #2 medium-grade, knotty pine, some of the humblest material on the market. He arranged for a company to pre-cut the lumber and sell it in packs as Metamobile. Naturally, one of these vintage 1974 kit tables sold for $14,400 at auction last fall.
Naturally, a gallery in Chelsea, Demisch Danant, just closed an exhibition of Metamobile furniture which they had made, and which they arranged for Mari himself to sign. Which seems to defeat several purposes of the entire Autoprogettazione concept, but that’s life.
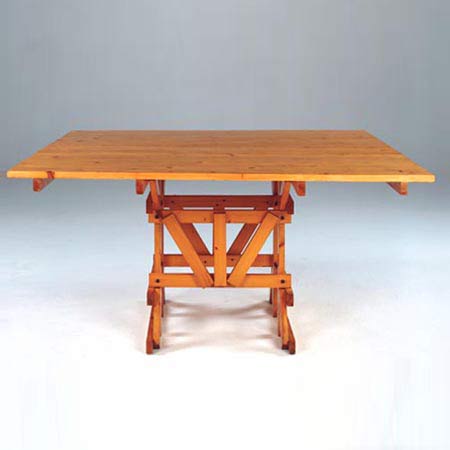
I’m looking for photos of the first Metamobile furniture I saw, which is still my favorite: In 2004, Rirkrit Tiravanija produced Mari’s square dining table [above] and some chairs in chrome-plated stainless steel. The pieces weighed a ton, but they were truly spectacular, like Koons picnic furniture.
Anyway, we’re just in the middle of moving our place in DC, which gives me the occasion to need a bigger, nicer dining room table. Mid-century modernism is too relentlessly tasteful; recent prices of “good” furniture make me laugh out loud. Though I’m an unrepentant Ikea fan, it only goes so far [i.e., no serious furniture]. Mari’s furniture feels like the perfect counterpoint to the homogeneous mega-catalogue stores: C&B, Pottery Barn, CB2, West Elm, etc. etc. etc.
So I’m thinking of getting the Truss Table [top] known as the EFFE Table. As a city dweller, I’d have to have it made, or at least have the lumber cut and finished and delivered for my own assembly.
An ex-pat design firm in Japan used sugi, Japanese cedar, to make their EFFE table. For me, I think it’s key to use Mari’s intended pine. So far, I’ve sourced two wildly disparate, but potentially interesting woods:
update: Those Demisch Danant pieces appear related to a series of 18 pieces put up at auction last June in Paris. Artcurial has a making of video, though they don’t actually show what they made. An EFFE Table went for EUR2,231.